HSS tools and Carbide tools are essential tools in the cutting industry. There are several things to know when you want to make a choice. HSS tools are high-speed steel tools. They are tough and have a high working hardness. Cemented carbide tools are more challenging, which is why they have a more appreciable lifespan than HSS tools. The characteristics of these tools lead to them being perfect for certain applications.
This article will expose you to what you should know about the HSS and Carbide tools. It would help you in making a great choice according to your task. (Video presentation)
Table of Contents
- 6 Things You Should Know
- 1. Composition:
- 2. Cuttin Speed and Feed Rate:
- 3. Drilling:
- 4. Machinability:
- 5. Heat Resistance and Rigidity:
- 6. Lifespan and Cost:
- Conclusion
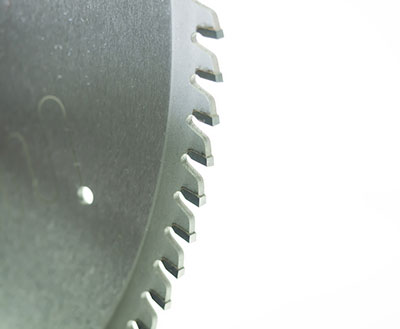
Figure : A circular material with carbide tip
6 Things You Should Know
1. Composition:
In the production of HSS tools, several elements are present. These elements have varying composition percentages. The most important is carbon; it is present in around 1-4% of the weight.
This carbon combines with one or two alloys to give the HSS tools. Depending on the type of HSS, these alloys could be different. It is from this combination that the HSS gets its toughness characteristic.
Tungsten and molybdenum are the most important of these alloy elements. About 10% of their addition increases the hardness and toughness of the HSS tools.
It also helps to maintain those characteristics when cutting with those tools at high temperatures. Other popfavouriteements include vanadium, chromium, and even cobalt.
However, cobalt increases the strength of the tools and wear resistance. It is why it is often added when manufacturers are producing HSS tools for high-end drilling applications.
Carbide by means the other hand has different compositions. Although carbon is present, it requires other types of alloys. The stability of carbide tools has dependent on the presence of these alloys/elements.
These elements are usually less electronegative than carbon. These carbide tools could be metal carbide or non-metal carbide. The metal carbide would be carbon with Cobalt, Tungsten, Vanadium, and Titanium.
The non-metal carbide would be carbon with boron and silicon. With these elements, carbide tools are exttoughd resistant to high temperatures.
The best and com typical lot is the tungsten carbide tools. They maxmaximisetting speed with the feed rate. It is why when in comparison with the HSS tool, carbide tools have a longer lifespan.
Figure 1:Hss tools with the chromium element
Figure 2: Carbide square plate with the tungsten alloy component
2. Cuttin Speed and Feed Rate:
Cutting speed is the difference in speed between the cutting tool and the surface of the material you are working on. Based on the composition of these tools, HSS tools cannot compare to carbide tools in terms of cutting speed.
On average, carbide tools are 5 to 12 times faster than HSS tools. This estimation could change depending on the material you are cutting.
The cutting components of the carbide tools have attributes that make them usable and fast for cutting.
The cutting speed of these tools is responsible for the heat that generates on the edges of these tools. You might be wondering about the benefits of high speed.
One of the benefiadvantagesat it extends your tool lifespan. Carbide tools have an extended lifespan because they reduce tool wear while cutting the right material at high speed.
After all, high cutting speed minimiminimisesng force. On the other hand, the feed rate is the distance the tool travels during a single spindle revolution.
It determines the rate the HSS tools and carbide tools remove materials and their finishing. The material you are cutting, the depth of the cut/drilling, and the size determine the feed rate.
The feed rate of HSS tools is considerably lower than that of the carbide tools. It also explains why carbide tools have a longer lifespan than HSS tools.
It is because of a high feed rate neutraneutralisesffect of chip thinning. It increases productivity while preventing rubbing, reducing the cutting tools’ lifespan.
Figure 3: A circular material with carbide tip
3. Drilling:
If your interest is in HSS or carbide drilling tools, it is best to understand how they work. HSS drilling tools have various uses. These uses range from handheld applications to short-period CNC machining. It is due to their low cost and toughness. They are the best drilling option for applications with less rigidity. These applications include handheld drilling, stack drilling, and even deep-hole drilling where a coolant supply is not present.
On the other hand, carbide drilling tools are used during high-volume end production. They are the best and fastest tools for drilling holes in metals. It is because they have a higher cutting speed and feed rate.
Figure 4: HSS and carbide types of drill bits
4. Machinability:
Machinability is the ease with which you cut/drill materials at a low cost. Another essential thing to know is the machinability of these tools.
Some HSS tools have low machinability. They are sound tools, and basic methods cannot make them machineable. It is due to their high carbon content.
The best carbon content to achieve high machinability is around 0.2%. In addition, the metal alloys like molybdenum and chromium in the HSS tools also decrease machinability.
Similarly to the HSS tools, carbide tools have considerably low machinability. It is due to the presence of tungsten, which abrades the cutting tools.
However, machinability between the two types of tools is not measurable. It is because many factors affect the machinability of tools. The usual way to access this characteristic is to compare common metrics like tool life, surface finish, etc.
5. Heat Resistance and Rigidity:
HSS tools and carbide tools have excellent resistance to higher temperatures. However, they differ slightly according to their composition.
With this characteristic, they can maintain their shape and sizes under compression. HSS tools have moderate resistance to heat deformation.
It depends on the coating of the HSS tools. The usual film for HSS tools is Nitride hard coating. It goes a long way in ensuring the tools can maintain their shape under high operating temperatures.
Carbide tools have high resistance to high temperatures. Unlike the HSS tools, with Nitride coating, carbide tools have Nitride hard coating small quantities of tantalum.
Tantalum can withstand almost 4000 degrees Celsius. It is easy to detect its importance in carbide tools. It explains their high-temperature resistance.
It is essential because carbide tools generate high temperatures during operations because they have high cutting speeds.
Rigidity, however, is the level of hard materials the tools can cut. The rigidity of the carbide tools is greater than the HSS tools. This edge increases the productivity of the tools.
Unlike the HSS tools, carbide tools can grind through tough materials for a more extended period without wearing out. HSS tools, too, could grind through hard materials but to an extent.
Figure 5: A carbide tool cutting metal
6. Lifespan and Cost:
With what we have read so far about HSS and carbide tools, we must point out their lifespan and cost. Although, with what you’ve read, it is quite easy to understand our choices.
As with all HSS tools, they wear out before carbide tools. However, it is essential to know this claim isn’t permanent. Still, it estimates how long they can maintain perfect shape while using them on standard materials.
Carbide tools have a longer lifespan because they operate faster, have the right heat resistance, and improve surface finishing. Another sound reason is the presa ence of cobalt in carbide tools.
The cobalt catalyzes by holding on the components of the carbide tools together. The HSS tools can also do this but to a lesser extent.
Since carbide tools have longer sizes for premium quality, they cost more than HSS tools. However, if you are on a budget, HSS tools would still give excellent results if you use them according to manufacturers’ recommendations.
However, this article does not describe which tool is better than which. You can make a choice base on facts and features. Whichever you buy, you will enjoy good results if you put it to use under standard conditions.
Conclusion
HSS and carbide tools have been significant in their composition, strength, machinability, and heat resistance features. These features enable them to have a longer lifespan.
In terms of quality, there is not much difference between the two types of tools. However, carbide tools differ slightly in heat resistance, which leads to their long lifespan and higher cost than HSS tools.
For your quality HSS and carbide, we at NCcuttingTools, have extensive experience in providing it to meet your expectations.
We use our advanced technology to provide you with scientific innovations by creating and providing you with the HSS and carbide tools for your cutting operations. Contact us for more information, and let us do business together.